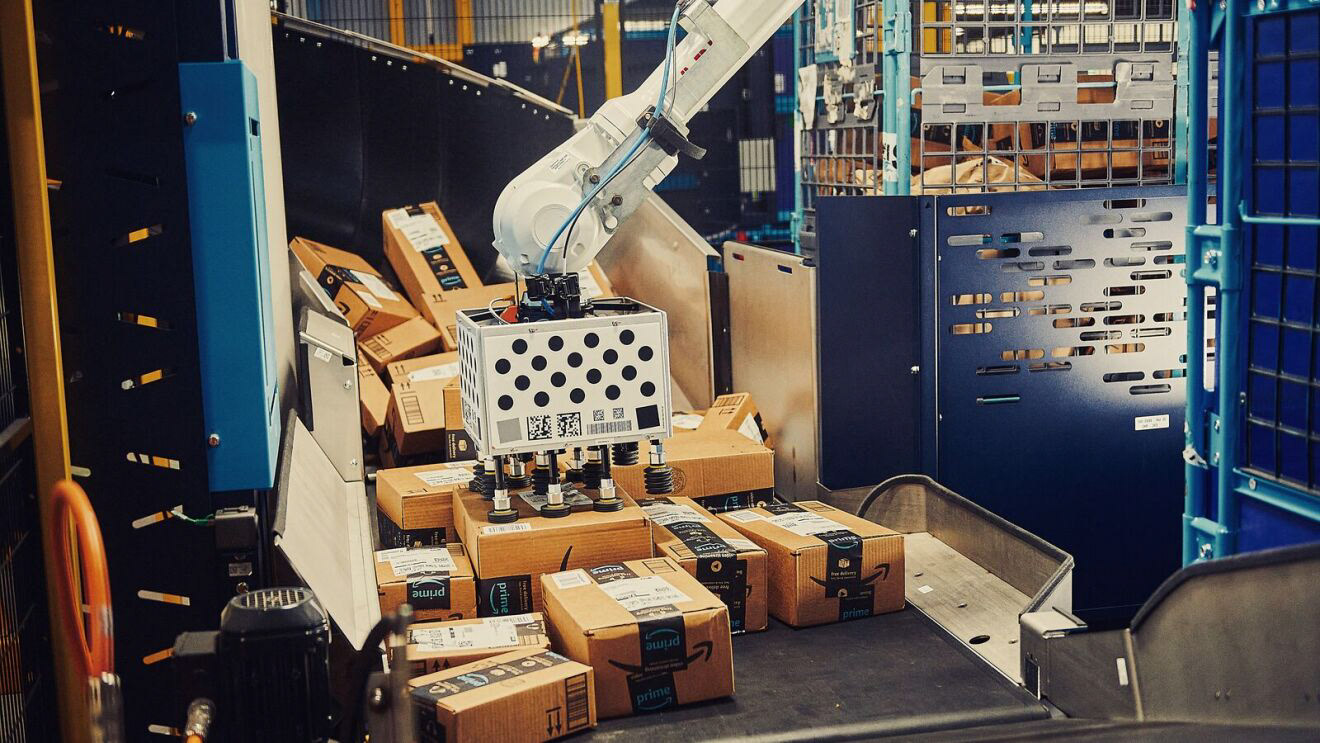
Amazon's Cardinal robot is a system that sorts boxes that are ready to be shipped and are on their way to delivery trucks. It stacks these packages in carts, strategically placing them based on size and weight, similar to a game of Tetris, utilizing the maximum volume of each cart.
My work on Cardinal was focused on optimizing the end-of-arm tool (EOAT). Cardinal's EOAT is a complex electropneumatic system that uses 12 individually controlled suction cups to lift packages weighing up to 50 pounds. Because of its intricate design, the EOAT contains hundreds of specialized parts. I explored a way to reduce this complexity by utilizing a central 3D-printed aluminum part. This approach enables many components to be printed directly into the part, reducing the part count by 87% compared to the previous design. By the end of my 6-month co-op, the optimized part was production-ready, and a pilot run was approved. When fully deployed, the ownership cost savings are expected to exceed $700,000.